Principle of Operation
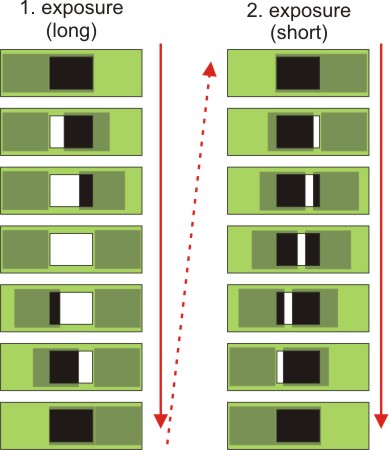
Sketch of two consecutive exposures. The first one (left) is long such that the shutter stays open for a while. The second one is short: The closing blade starts moving while the opening blade is still in the aperture resulting in a moving slit. Even for the largest shutter (600mm) blades move in less than 1sec across the aperture.
Symmetry
The mechanics is based on two carbon fiber or sandwich type blades moving on a pair of linear ball bearings and driven by two stepper motors and toothed belts. Bonn shutters are built with a high degree of symmetry and unlike most other shutter types they don't have a preferred direction of movement. Consequently for consecutive exposures the shutter blades move first from left to right and then from right to left. The control electronics hardware design is symmetric as well. It consists of two identical microcontroller systems - one for each shutter blade.
Low Accelereation
A camera shutter has to guarantee precise exposure times. Moreover the exposure times have to be the same at each point in the focal plane, i.e. exposures have to be homogeneous. Most shutters (iris type, sector disk, slit type) try to achieve these goals by high speed operation, at least if short exposure times are required. High speed implies high acceleration and deceleration. The corresponding energy has to be absorbed by the device - for spring actuated types usually within a very short (msec) breaking period. It is therefore clear that lifetime of the shutter device and vibrations induced to the whole instrument by the shutter operation are usually major issues.
The Bonn shutters are impact free, low acceleration (i.e. low power) devices. Their lifetime is among the less critical aspects. As an example, the acceleration and deceleration of the shutter during opening (7m/sec^2) are about an order of magnitude below the radially outward acceleration of a typical 60-100mm iris typ shutter (opening time about 30msec), not to speak about the impact like deceleration of the latter.
Precision Control
Instead of driving the shutter blades at high speed/acceleration the 1msec timing accuracy is achieved by a simple yet very precise motion control of both blades: The generation of every single stepper motor micro-step (25 µm per step) follows exactly a time table which is derived from a given velocity profile and stored in µC RAM. Both blades are driven with identical time tables (i.e. velocity profiles), a prerequisite for homogeneous exposures. The trapezoidal velocity profile is software programmable.